30/1 - Quintuple the cheesiness
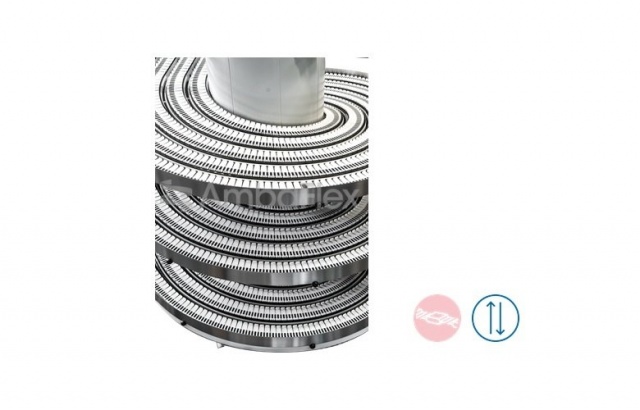
An American multinational confectionery, food, and beverage company faced a challenge transporting cheese coming from numerous separate production lines into a single packaging machine on a different level.
The reason they wanted all five lines to converge into one packaging machine was to keep the machine fed, even if one or two lines experienced stoppages. They considered the traditional option of straight conveyor tracks, but they either take up too much floor space or, with a steeper angle of inclination, increased the risk of sliding or falling products. A regular spiral conveyor wasn’t an option either as all five lines had to be driven individually.
AmbaFlex engineers gladly took on the challenge as they had more than enough experience with multi-track spirals. This project turned out to be unique though as the tracks were all narrow type belts, which kept the size of the spiral down, but posed a real technical issue when adding six individual side-guides and all five drives.
With clever engineering, the AmbaFlex team figured out the optimal position for each drive, connecting the tracks to the production lines while separating the different lines of cheese. This kept the packaging machine working on its maximum throughput even if one or two production lines suffered from stops or repairs.
One more proof of AmbaFlex’s leading position in Spiral Conveyor Solutions!