28/5 - Keeping it Fresh and Dynamic
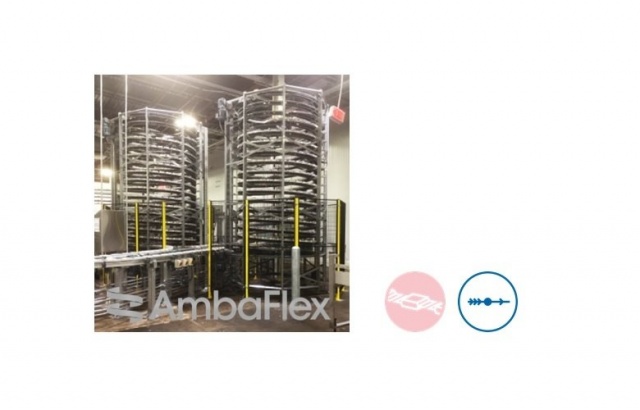
The ‘Ready meals’ formula, meals that are freshly made and packaged in plastic containers, is rapidly gaining in popularity. A producer of these types of foods hailing from the USA currently has three production lines operational which are all working at maximum capacity. Because of the increase in demand, it looked like the company needed to invest heavily in a 4th production line just to keep up. Fortunately, they found out there were still some options left in regards to optimizing the efficiency of their existing lines.
Each production line consists of a food preparation step where the fresh ingredients are prepared and put in plastic packs. After which the vacuum top-seal machine closes and seals these packs within a specially conditioned atmosphere to keep them fresh. And finally, the individual packs are then packaged into larger cases for easy transport.
The issues that plagued the process flow were centered around the case packer. These types of machines are prone to disruptions and even though they are often quickly resolved they also force the top-seal machine to a stop. Especially that factor, the stoppage of the top-seal machine, is problematic as a whole series of boxes have to be written off as waste as the special conditioning process only works when the whole process is running at full speed. The problem is that these types of products have a difficult shape for and tend to give accumulator systems a lot of trouble, up until now.
The answer to this was the use of a set of AmbaFlex AccuVeyors AVh machines, a unique solution within the world of accumulation. Because these spirals only use a single belt, there’s no need for a product transfer unit or, as used in low-end accumulators, systems that work on pressure. The products stay on their respective place on the belt throughout the whole accumulation process. There is no pressure put on the product or is it touched in any way while keeping the process wholly dynamic and on a first-in, first-out principle.
Each AccuVeyor can store up to 400 top-seal packs. When more products are coming in than going out, which is the case in a down-stream breakdown of the packer or when the line is starting up, the belt within the AccuVeyor increases in length and moves upwards. When it’s the other way around; when more products are going out than in, because the case packer is faster than the top-seal machine, the AccuVeyor releases the stored packs and the belt moves down again.
An optimal balance that gave the customer a 30% increase in their efficiency. A quick calculation reveals that a 30% increase in efficiency for each of the three lines results in an increased production that would match the extra line they initially wanted to build, which makes the return on investment for the AccuVeyor AVh machines only a few short months.
One more proof of AmbaFlex’s leading position in Spiral Conveyor Solutions!