11/2 - Cutting it down to size
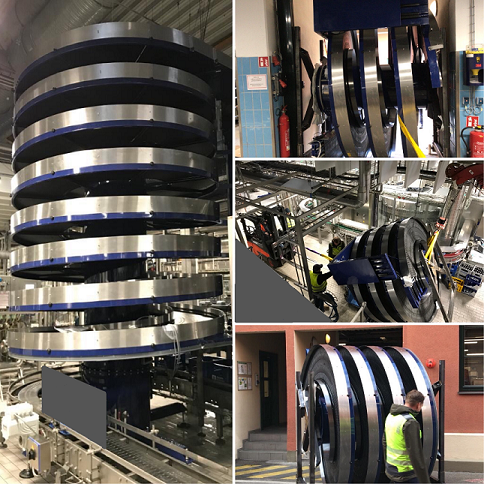
Many traditional breweries are located in beautiful, timeless buildings that carry a lot of history. Nobody wants to risk doing anything that could potentially damage them in any way. This creates problems though, when new and updated machinery needs to be installed to keep the brewery competitive. AmbaFlex, having the smallest footprints in combination with its modular design, had the perfect solution.
AmbaFlex recently got an opportunity to show their innovative thinking skills when an order came in from one of these types of breweries. The customer needed to upgrade an existing layout. They wanted to connect a new-glass depalletizer to an additional line, essentially giving the depalletizer the option to feed both of them at the same time. To accomplish this, they had to elevate their new glass to a higher level.
Depending on the surroundings, getting new equipment in safely can be difficult. A common way to do this when access is limited is by opening the roof and using a crane to lower in the parts. But because of the delicate, traditional factory roof, this wasn't an option. Meaning the parts had to go through the regular factory doors.
Besides having a smaller footprint than other spiral manufacturers, the AmbaFlex SpiralVeyors are genuinely modular. While other manufacturers are forced to build the whole machine inside, easily taking weeks to finish, AmbaFlex is done in two days. They first build and test the spiral in the assembly hall, making sure everything works perfectly. After which the spiral can be cut in smaller sections and quickly reassembled at the customer. Through this method, the AmbaFlex SVm found its way into the hall without any issues and was up and running in no time.
One more proof of AmbaFlex’s leading position in Spiral Conveyor Solutions!